Automated Finishing Systems Offer a 'Life-Changing' Paradigm Shift
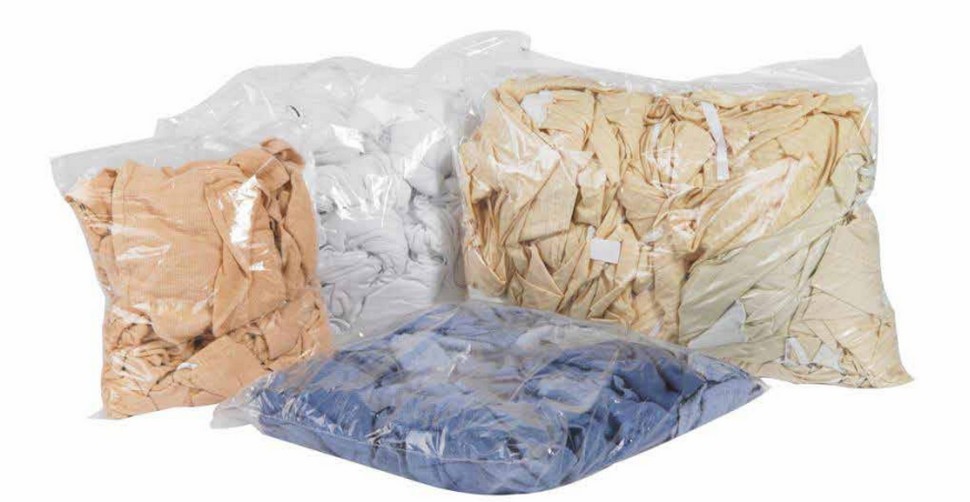
By Barbara L. Barnes
In Hollywood, at the conclusion of filming the director yells "That’s a wrap!" In the laundry industry, we call it packout. Laundry processing concludes in the final grouping and presentation of goods to the customer. Just as in plating a gourmet meal, linen presentation greatly effects the customer’s perception of received quality and value. Consequently, the laundry industry slowly adopts changes to the finishing process’s steps.
Laundries have used automated folders/ stackers for sheets, pillowcases, tabletops, napkins and larger towels for many years. Although machine folded and counted, employees individually secured bundles with string, banding, or poly wrap. Laundries continued to hand count, fold, stack and bundle small pieces such as shop towels, bar towels, kitchen towels, grill rags, microfiber items and washcloths.
Enter the paradigm shift for both laundries and customers in how they handle and receive goods. Equipment (such as the Autobag Ergocon Textile Packaging System, Rennco Vertic L-PP Laundry Bagging System and Felins® Automatic Shrink Wrapping System) has added to laundry finishing options. Many laundries now feed items into poly bags or heat-seal wrap bundles automatically. In light of this change, what considerations, challenges and benefits have owner/operators experienced?
Quality finishing requires expensive, exacting workers who are difficult to find. All six laundry executives interviewed for this article cited labor concerns as the initial stimulus for adopting finishing automation.
Depending on the markets served, most
owner/operators described replacing
manual processes with a bagging system
for shop towels, bar towels, kitchen towels,
grill wipes and microfiber towels/wet
mops. Dave Manter, director of operations,
Balfurd Linen Service, Tipton, PA
says they bag "anything our customers
will let us." Tyler Burke, plant manager,
Loop Linen Services Inc, Westwego, LA,
adds to the list enviro napkins for their
lesser-end eating establishments. Todd
Deaton, senior vice president, uniforms
and linen, Wildman Uniform, Warsaw,
IN, says they bag all of their "fluff" goods including bath towels, massage
towels and wash cloths. Since they service
many truck stops, Deaton says that
the motel/hotel market may not accept
the practice, whereas their clientele does.
The towels "fluff up fine."
The consensus view among these laundry executives is that labor savings was the initial reason for their move to finishing-side automation. Burke describes the need to "engineer people out" to control costs. Deaton also cites the challenge of finding qualified people to work amid a fiercely competitive market for labor in Northern Indiana. Greg Hersey, vice president, Superior Linen Service, Tacoma, WA, adds that the increased minimum wage in Washington state ($12 per hour; moving to $14.25 in 2022) lead his company to look for ways to automate to "get back to where we want THAT’S A WRAP! FINISHING-SIDE AUTOMATION March 2018 § Textile SERVICES 33 to be" in terms of labor costs. The state’s minimum wage is slated to rise to $14.25 by 2022.
Paul Kramer, chairman, City Uniforms and Linen, Findlay, OH, describes how after the economic challenges of the 2008-’10 Great Recession he "saw a narrower version of who we were. If we were going to sell on value, we needed to be efficient." Kramer claims that he reduced labor by eight full-time-equivalent employees (FTEs) on the first day after he completed his bagger installation. Hersey says he saved three FTEs. Steve Marcq, director of business development, General Linen Service, LLC, Somersworth, NH, says he saved two FTEs. Kramer quips that the equipment "shows up to work every day and I don’t have to pay health insurance!"
Manter adds that, "Preparing bar towels was taking up a significant portion of our time so the conversion was a no-brainer." Burke says that when hand folding they were processing 30,000 towels a day, which took all day between two shifts. Now they are bagging around 40,000 a day in one shift.
Labor savings and production increases drive return of investment (ROI) evaluations. Kramer estimates a four month ROI, while Hersey anticipates a 12-13 month ROI, thus making the bagger a simple purchase decision.